STRUCTURAL DIAGNOSTICS
Structural knowledge and diagnosis of buildings through monitoring.
STRUCTURAL
MONITORING
Monitoring is the process of characterizing the structure to obtain information on its performance level in order to maintain high levels of safety and efficiency over time.
The aim of monitoring is to investigate the actual behavior of the structure (reducing uncertainties due to intrinsic variabilities in materials and actions) in order to optimize maintenance and any necessary restoration interventions based on objective data. Periodic monitoring during operation allows for the definition of a dedicated and effective maintenance plan.
The diagnostic system is based on the combination of mathematical models and innovative, widespread, and minimally invasive monitoring, capable of providing the user with real-time information on the state of the structure and its evolution.
The key control parameters are related to the global stress-strain evolution and dynamic characteristics of structures, evaluated through a mixed approach of "Model Driven" (thresholds based on calibrated structural physical-mathematical models) and "Data Driven" (anomaly detection thresholds for identifying unfavorable trends) to assess the possible occurrence of damage-related phenomena. The measurement system combines MEMS technology and a cloud-based or local server computing architecture capable of automatically acquiring, processing, and storing data. The structural engineer compares the field measurements of structural parameters with the expected results from the finite element model of the structure to determine attention and alarm thresholds and detect any structural criticalities through advanced algorithms. If these critical thresholds are exceeded, or if there are anomalies in structural behavior, communications are activated to the responsible figures of the managing entity.
For the monitoring system, a data processing protocol has been developed to transform the sensor readings into "consistent" data, which is significant for subsequent numerical modeling phases. The data collection and transmission network is characterized by continuous and automatic acquisition of sensor readings by a gateway, transmission at predetermined time intervals of data and system statistics to the cloud platform for storage and subsequent processing. In the cloud platform, the data processing involves a post elaboration that includes all the treatment procedures of the detected measurements, in order to obtain data that is free from any errors or environmental influences and can be used for structural analysis. The processed data is used by the engineer to perform mathematical and structural analyses.
DATA
MANAGEMENT
Data from sensors are stored on a dedicated Cloud database. In the Cloud infrastructure, all the technical information characterizing the structure under examination is stored, such as geometry, sensor identification, sensor arrangement in the structure, etc. Once the data is collected, it is processed and transformed into "structural" data.
Data processing includes all the procedures for treating the readings in order to obtain a data set that is purified of any environmental influences and can be used for structural analysis. In particular, a specific algorithm processes the raw data, extracting sensor readings from the database at a predetermined time frequency, and returns a set of preliminary treated data, which is also stored on the database for subsequent use.

STRUCTURAL
DIAGNOSTICS
MODEL-DRIVEN APPROACH
To determine the expected behavior of the monitored structure using a "Model Driven" approach, the post-processing engineering activity involves implementing a finite element numerical model of the structure. The modeling is aimed at identifying the initial deformations and stress state, assumed to be present at the start of the monitoring and evaluated based on information on geometry, materials, and the evolutionary history of the structure.

Where possible, a specific load test is performed for each monitored structure to validate the structural monitoring and diagnostic system.

The validation of the theoretical assumptions, occurs through appropriate calibration of the developed finite element calculation model (Model Updating), to which the evaluation of any future degradation of materials or any distress occurring during the operational life of the structure is referred.
By comparing the expected values of the significant parameters monitored obtainable from the finite element model with the values of the same parameters collected during the load test, the stiffness and boundary conditions of the Digital Twin are calibrated.
By comparing the expected values of the significant parameters monitored obtainable from the finite element model with the values of the same parameters collected during the load test, the stiffness and boundary conditions of the Digital Twin are calibrated.
The diagnostic and monitoring activity is based on determining thresholds with which the collected measurements are compared. The set threshold levels are based on the values taken by the measured quantities (deformations, displacements, rotations, etc.), differentiated by the type and position of the sensor within the different types of monitored structure and/or element.
The thresholds thus defined are the reference for the analyzed structure.
The thresholds thus defined are the reference for the analyzed structure.
Data Driven approach
To optimize the extensive and widespread application of monitoring on structures, a "light" monitoring approach can be applied to those main structural elements to which the typical behavior of the monitored structure can refer (e.g. in a viaduct with numerous similar spans, some representative spans are monitored, representing the others in terms of geometry and static scheme). In this case, the structural characterization performed on representative portions of the structure is taken as an example of the typical behavior expected also for the portions/elements not subject to complete numerical analysis and modeling.
This monitoring takes place according to predominantly data-driven procedures, following adequate data processing after an initial training period, through anomaly detection checks that are functional to the identification of anomalies compared to a standard reference trend for the monitored parameters.
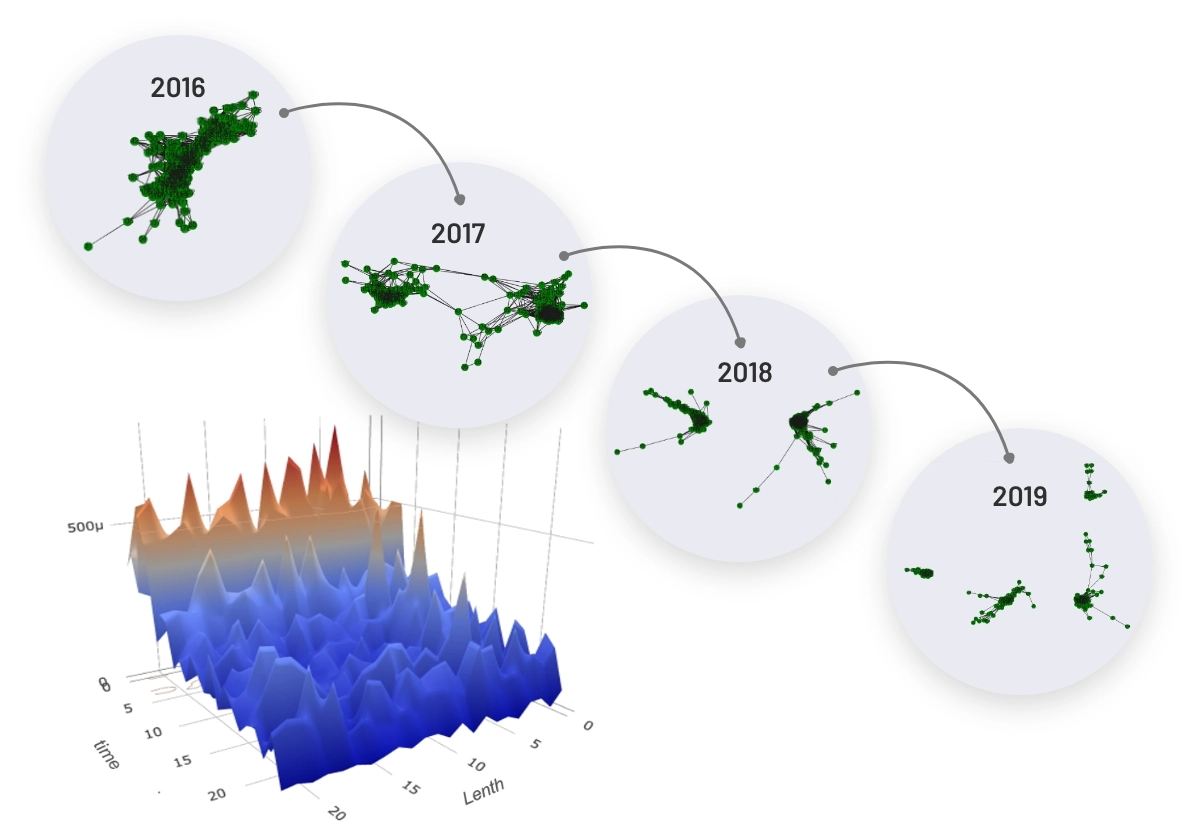
CONTROL PROCEDURES AND
CONTINUOUS ALERTING
Data from sensors, processed through ad hoc procedures that transform raw data into the relevant physical parameter, are compared in near-real time with pre-set threshold values to detect any structural issues through advanced ad-hoc algorithms.
An appropriate communication protocol is defined for any detected anomalies, associated with a decision-making process to implement preventive actions to maintain the structure's safety level and optimize maintenance operations.
An appropriate communication protocol is defined for any detected anomalies, associated with a decision-making process to implement preventive actions to maintain the structure's safety level and optimize maintenance operations.
The proposed monitoring system can be integrated with the Operator's inspection and monitoring management systems, with the ultimate aim of supporting the Control Center by providing diagnostic information useful for the correct management of the maintenance activities of the works of the same network of infrastructure.
SHM SOLUTIONS
Approaches based on MODEL DRIVEN and/or DATA DRIVEN methods. Continuous on-site and on-cloud monitoring of data from the monitoring system. Structural engineering analysis to define threshold levels that activate automatic alerting.